The press brake bending machine mainly performs straight-line bending of the plate. By using simple molds and process equipment, the metal sheet can be pressed into a certain geometric shape, and it can also be processed by stretching, punching, punching, and pressing corrugation. In actual production, the CNC press brake machine is mainly used to realize the bending of various geometric shapes of metal boxes, box shells, U-shaped beams, and rectangles. Its processing has the advantages of high bending straightness, no tooth marks, no peeling, no wrinkles, etc.
With the continuous development of CNC bending machine manufacturing technology, its advantages such as high positioning accuracy, convenience, zero-activity disturbance compensation, and good consistency of processed products have become increasingly favored by the majority of sheet metal manufacturing companies. However, with limited wishes, how to make better use of the bending machine and give full play to its functions and advantages has become a problem that manufacturers using CNC press brake bending machine pay attention to and urgently need to solve. In the long-term manufacturing and use process, Zhongrui has effectively expanded the functions of the bending machine and accumulated experience through the addition of auxiliary tooling, the transformation of existing molds, and the flexible use of the site. This article takes Zhongrui's CNC press brake machine DA66T as an example and introduces the skills in use in detail.
Add auxiliary tooling
If you want to make the press brake machine tool flexible and easy to use, adding auxiliary tooling is essential. The increase of auxiliary tooling can not only expand the processing range of the CNC bending machine tool but also improve the processing efficiency.
1) Transition plate (assisted middle plate for rapid mold)
The opening height of the bending machine refers to the distance between the upper and lower worktables. Because the CNC bending machine DA66T has a larger opening height, consider using a large opening to expand the processing range. As shown in Figure 1, adding another transition plate to the original transition plate can increase the side bending height of the part (up to 85 mm), so that deep processing with higher side bending edges can be carried out. The self-made transition board can customize the width of the transition board according to your own common parts, and it is most suitable for processing small width parts with higher bending edges on both sides.
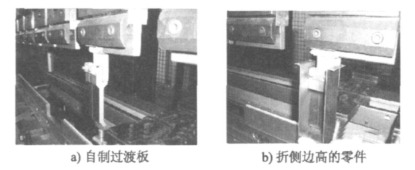
2) Corner of the front panel
As shown in Figure 2, the front of the machine is equipped with a corner, which can place small parts and reduce the time to take parts. At the same time, a small worktable is installed to facilitate the processing and collection of tiny workpieces.
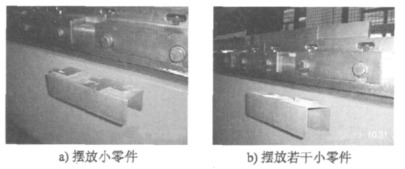
Make full use of the mold
The use of the CNC press brake bending machine mainly relies on the upper and lower molds. If the number of molds is small and the application is not flexible, the processing range of the machine tool will be greatly restricted. Therefore, under fixed conditions, how to maximize the function of the existing mold through optimized combination and partial transformation is a problem that every machine tool user must think about. The following is the expansion function that we use in use by changing the mold of the CNC bending machine Introduction.
1) Upper die grinding tip R
When the upper die is used for a long time, its tip wear will change irregularly. The height of the mold changes and the bending accuracy cannot be guaranteed. By grinding, correcting the tip R, and matching with a larger V-shaped groove, thick plates can be folded. This prolongs the service life of the mold.
2) Change scrap molds to achieve leveling
In the absence of a composite bending die, solving the forming problem of how to press the dead edge is an example. The dead edge is a bent shape in which two layers overlap each other, and is usually used for reinforcement. Generally, the board over 2 mm has almost no press dead edges. Press the dead edge needs to be formed by a compound bending die, and it must be divided into more than two processes to be formed.
The commonly used method is to use a compound bending die, as shown in Figure 3. In the first step, the material is folded to 30°, and in the second step, the 30° bend angle is placed at the front end of the compound mold, and the material is folded into a dead edge. But we do not have a composite bending die, only a 30° acute angle bending die. Complete the first step of the composite bending die with the existing mold, and the second step can only find another method. In the second step, the upper and lower molds are both flat. After analysis, the middle part of the existing double v-groove lower mold can be used as the plane part, and the upper mold is looking for a plane. Take out the existing scrapped upper mold and grind the knife edge into a flat style, thus solving the forming problem of the press the dead edge.
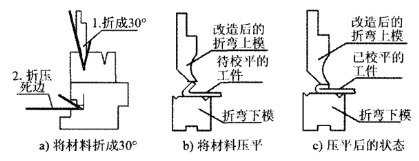
Using this set of modified molds can also be flattened. In actual processing, machine tool operators sometimes make mistakes, including bending edges or bending dimensions that are not equal. In the case where the surface requirements of the part are not high, it is a pity to scrap the part, only to knock the bending edge flat. Knockout is very laborious, but it can be easily leveled by using the above mold combination. The parts can be easily pressed by hand to the upper and lower molds, and then the parts are flattened by the CNC bending machine.
Skills during operation
1) Placement of bending dies and processing materials
When arranging the plan, the following factors should be considered:
a. Arrange materials of the same thickness together;
b. Arrange the molds of the same model together;
c. Molds of similar shape are arranged together.
This can reduce the time and frequency of mold replacement.
2) Right-angle positioning of narrow and small parts
When the bending part is narrow and long, it is not easy to locate. During processing, it often happens that the post-decision positioning, and the bent part is easy to tilt. Therefore, using the method used in Figure 4, the mold is glued to the lower mold to ensure a right angle. When bending like this, the part is not easy to tilt.

3) Bending of triangular parts
When the bending parts are bent, the sharp-angled parts are not easy to be close to the rear rule. Generally, when the smallest dimension L ≤10 mm immediately rear rule, the positioning device should be considered. In actual work, design and process are easy to be neglected, and such problems often occur. When processing, according to the size of the part, it is determined that a single piece is aligned with the bending die and the double piece is aligned with the backing.
4) Add thin plate R
Due to the different needs of customers, the required R value on the bending edge is also different. In the process of processing, for parts that do not require high dimensional accuracy, use a backing plate to increase the R value so that the required R value can be obtained after bending. According to the design requirements, R refers to the relationship between V and inner R to select the plate thickness and fold it into the shape shown in Figure 5. When in use, use a clamp to clamp the upper mold. This method is easy to use and can be used in multiple layers.
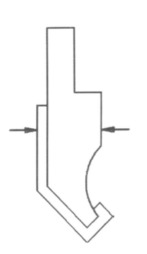
5) Single part and multiple mold settings
Zhongrui used DA66T CNC bending machine with 2 hydraulic cylinders as a demonstration. Tried the multi-mold setup shown in Figure 6, that is, the upper and lower molds of the same model are installed in sections at one time, which can complete the processing of several bends of the entire part, reducing the time of mold installation and repeated handling of parts. At present, the equal height bending upper die has appeared on the market. The height of the upper mold is all uniform, and molds of different shapes can also be used on the same table. In this way, it is possible to perform segmental bending of different molds.
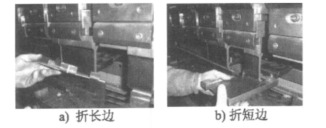
6) Program records of typical parts
After the typical parts are processed, the processing parameters should be recorded in time, and the program should be stored in the storage area of the bending machine with the part drawing number, so that it can be reused in the future, greatly reducing a series of preparations before bending. You can also make a table, which contains the specific settings of the part name, drawing number, graphics, material, and bending parameters. The table is divided into steel plates, aluminum plates, and stainless steel plates. Each type is distinguished by the thickness of the material. The time it takes to find typical parts will be reduced. If combined with the process card, this is a very complete processing instruction. Even new employees with little experience can follow the prompts to process parts.
7) The mold length is not enough to bend in sections
In on-site processing, it often happens that the length of the mold is smaller than the bending edge. Because many special molds are determined according to the use of fixed products, the method of segmented bending is used when the length of the mold is less than the bending edge. Where the length of the mold is close to the bending edge, tear the edge perpendicular to the bending edge, and then fold the bending edge to the required size in sections. Figure 7a is the left half of the bent part, and Figure 7b is the right half of the bent part.

8) Using stud on back gauge to position
When the size of the bent part is large and use back gauge to position, the parts often sink due to its own weight, the hand-held part is short, and the operator is not easy to hold the workpiece. In order to ensure the level of the parts, an operator must be arranged at the rear rule to hold the parts to a level state by hand. Therefore, when processing such parts, 2 operators must be arranged. In the work, it is found that the back gauge can be lowered to a certain size, and the studs on the back gauge are used for positioning, and the parts are placed horizontally on the back gauge. This not only reduces the number of operators, but also effectively guarantees the machining accuracy.
9) Deep closed shape bending
In actual processing, deep closed shape bending processing can be used flexibly. In the absence of a closed-type deep bending die, when bending the parts as shown in Figure 7, the clamping state shown in Figure 8 is adopted. Separate the transition board, the distance is slightly larger than the width of the part, and the size is allocated reasonably, and two parts can be bent at a time.
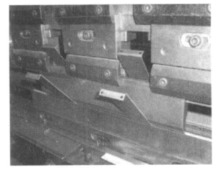
The processing methods and techniques introduced above can solve the processing problems of a large number of similar parts in products, and are very suitable for the development of products with multiple varieties, small batches and short production cycles. Through these methods, not only can the expenditure of tooling costs be saved, but also the production and processing cycle can be shortened, the production cost is reduced, and the product quality is improved. These processing methods and use skills can also be applied and promoted on CNC press brake bending machines with similar structures.